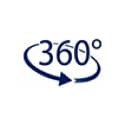
VISUALIZE IN
360°
Intelligent Non-Stop Flight Stamping.
High productivity, real speed of up to 60 m/min.
PE 400.3 ESQUADROS® PURLIN ROLLFORMING MACHINES
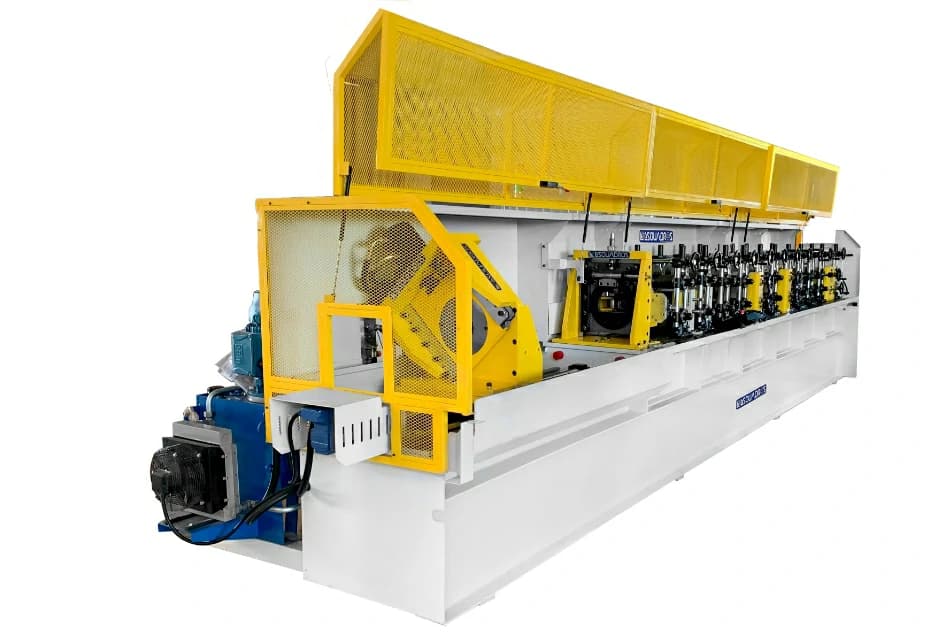
INNOVATIVE STRUCTURAL PROFILE TECHNOLOGY
FLEXIBILITY AND PRODUCTIVITY FOR MANUFACTURING STRUCTURAL PROFILES IN ACCORDANCE WITH NBR 6355:2012
The Purlin Rollforming Machines developed by Esquadros® has innovative and exclusive technologies for the manufacture of U and stiffened U profiles (U and C),, such as bearing synchronism, high productivity with a real speed of up to 60 m/min, cutting technology with knives that do not generate chips and the new intelligent flight stamping module.
The Esquadros® Purlin Rollforming Machines, model PE400.3, covers the thickness range from 2.00 mm to 3.20 mm, manufacturing profiles from 2" to 8" (from the U-45x17 mm profile to the C-200x75x25 mm profile), with coils weighing up to 6 (six) tons.
The profiles are produced with dimensional and geometric tolerances in accordance with the Brazilian standard NBR 6355:2012 , with high quality in the cutting and surface of the profiles, meeting even the strict quality standards required by steel distributors.
It is certainly the best cost-benefit solution on the market , as can be seen from the dozens of machines installed and in operation. More productivity and reduced operating costs, increasing the profit per ton processed.
The quick changeover of the conformation tooling on the Esquadros® machine is up to 4x faster than the conventional system , thanks to the synchronized height adjustment of the upper bearings, which provides very fast setup.
Find productivity with the Esquadros® Purlin Rollforming Machine: non-stop cutting through servomotor flying cutting and German SEW® drives that reach the real speeds of up to 60 m/min. .
Esquadros® is launching its exclusive "INTELLIGENT FLIGHT STAMPING" technological innovation on the market, which stamps already formed profiles non-stop with maximum precision and productivity, using compact, vertical and lateral stamping modules. It is possible to stamp holes, oblongs and special cut-outs for the production of a wide variety of profiles, such as: metal purlins for civil construction with mounting holes; profiles for the structure of photovoltaic panels (solar energy generation); among others.
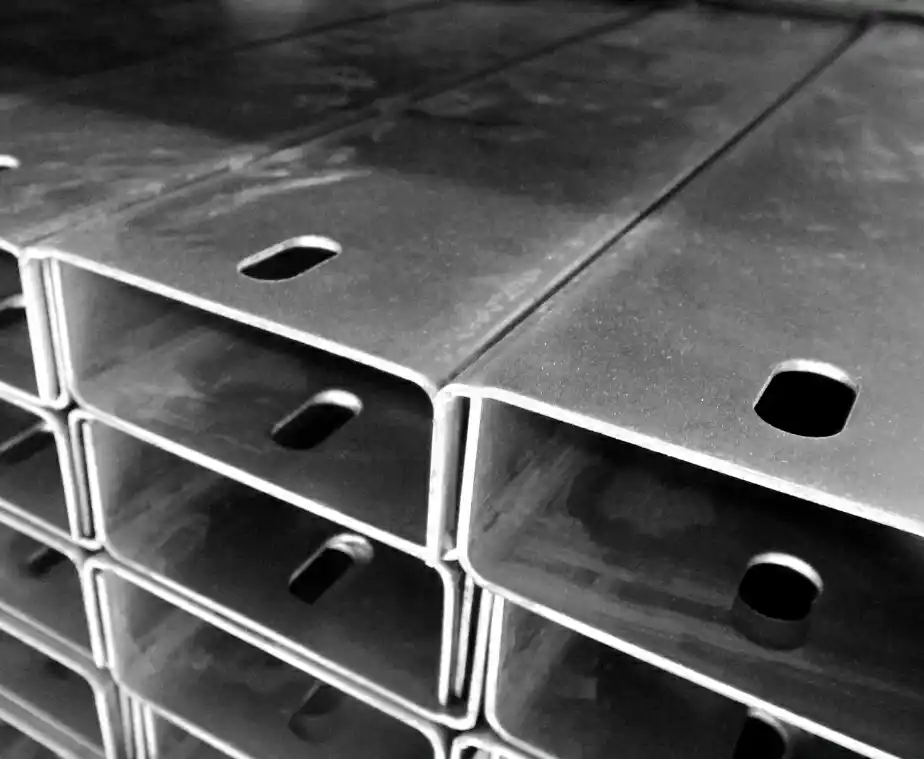
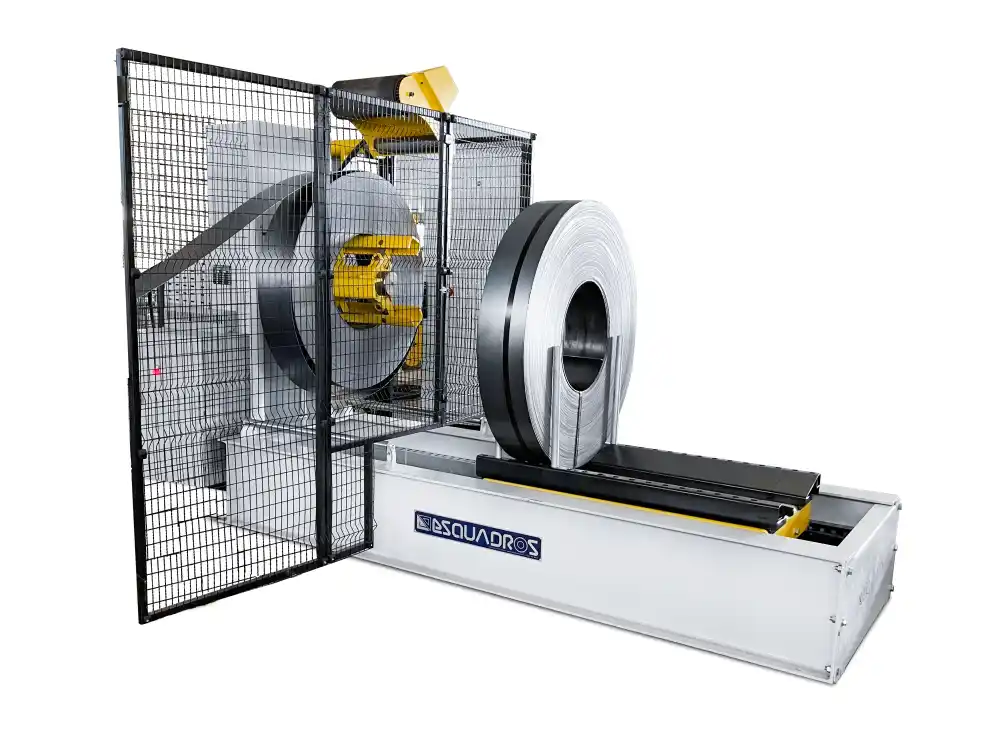
Total quality in the end product and elimination of material waste with Esquadros' cutting technology, with knives that do not generate chips or scrap. . The guillotine knives are made from D2 tool steel, with a cutting profile cut by wire electroerosion with a receiving angle, for a perfect cut and no burrs.
The line has a flexible design, with accessories and options capable of increasing productivity and reducing setup times, meeting real processing needs and meeting the requirements and particularities of each customer.
Structural profiles with different sections and dimensions, including special profiles, can also be produced following technical analysis by our applications engineers.
Complete after-sales service with responsiveness, total support for your business throughout the product's life cycle, service by technicians and engineers with experience and specialized knowledge, high availability of parts and services.
Start-up and technical handover of the machine, as well as all operational training, are carried out by our technical team in person at the customer's premises.
PURLIN ROLLFORMING MACHINES FOR MANUFACTURING “U" AND STIFFENED "U" PROFILES
.webp&w=3840&q=75)
“U" PROFILE
STIFFENED "U" PROFILE
PURLIN ROLLFORMING PE 400.3
“U” profile | STIFFENED "U" PROFILE | THICKNESS |
---|---|---|
A x B | A x B x C | Minimum - Maximum |
50 x 25 | 50 x 25 x 10 | 2,00 mm - 3,00 mm |
75 x 40 | 75 x 40 x 15 | 2,00 mm - 3,00 mm |
100 x 50 | 100 x 50 x 17 | 2,00 mm - 3,00 mm |
125 x 50 | 125 x 50 x 17 | 2,00 mm - 3,00 mm |
150 x 60 | 150 x 60 x 20 | 2,00 mm - 3,00 mm |
200 x 75 | 200 x 75 x 20 | 2,00 mm - 3,00 mm |
ESQUADROS® QUICK-CHANGE SYSTEM
Understanding the importance of operational flexibility for a machine that must produce different profiles, the Esquadros® Purlin Rollforming Machine has a quick change system for the conformation tooling, which is up to 4x faster than the conventional system.
It has synchronized upper bearing height adjustment providing very fast setup. The height adjustment of the upper axis is made by the simple movement of a flywheel, which activates 2 (two) boxes with precision reducers, coupled and interlocked, to ensure parallel and uniforme rising/lowering at each conformation stage, requiring less experience and time of the operator to make adjustments of the thickness variations of the profiles.
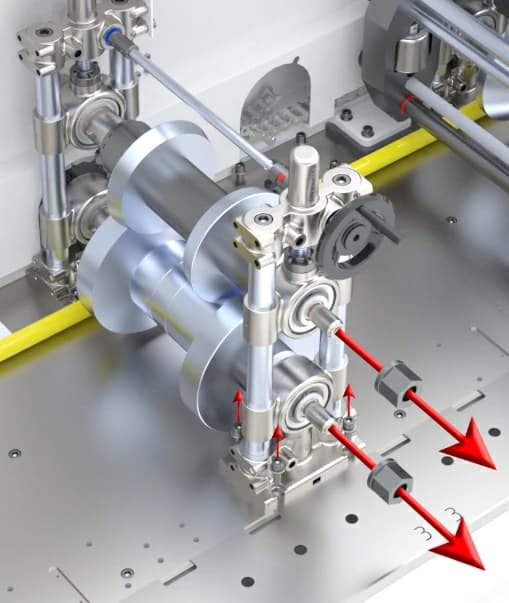
Picture 1- Conformation stage. Removal of the fixation components.
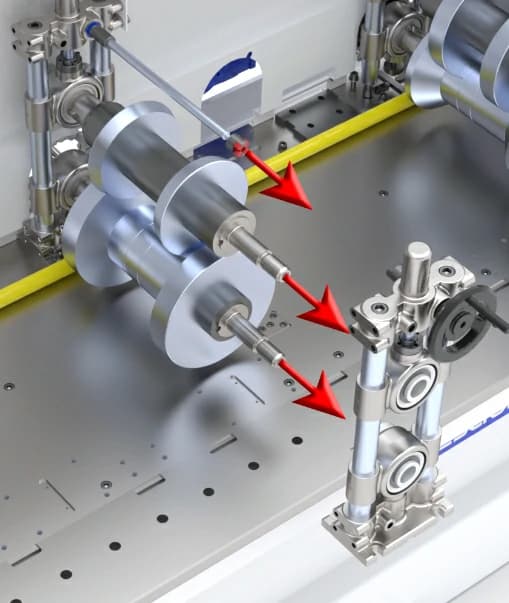
Picture 2 - Lateral uncoupling and disassembly of the bearing.
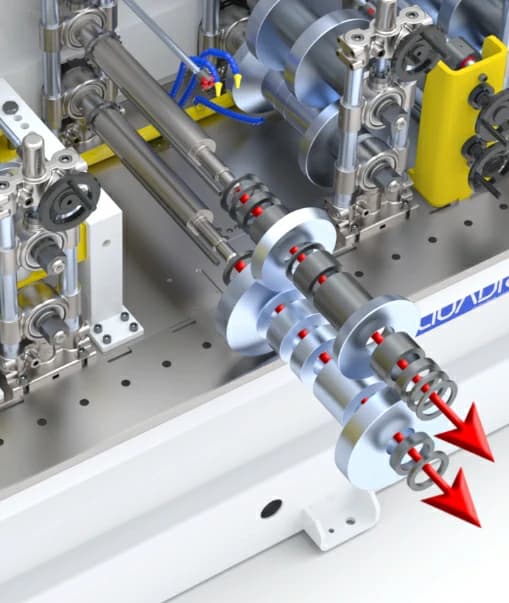
Picture 3 - Assembly of the cylindrical tooling. Only the tooling abutment on the axis abutment ensures that the machine is ready for production, not depending on the operator for manual alignments.
PRODUCTIVITY OPTIONALS
DECOILER
All the options for the best possible performance in the decoiling operation, with features such as:
• Motorization and intelligent electronic speed control of the decoiler;
• Hydraulic expansion of the decoiler mandrel for automatic coil clamping;
• Peeler pressing arm with motorized roller;
• Coil loading trolley;
• Entrance table;
LINE PERIPHERALS
Selection of accessories and options that facilitate operation and increase the performance of the set:
• Cutting and welding (splicing) station for the ends of the strip;
• Vertical or horizontal strip accumulator;
• Straighteners and electronic strip feeders;
• Stamping bench prior to conformation;
• Stamping modules in intelligent flight without stops (vertical and lateral);
• Semi-automatic and automatic bale stacking modules;
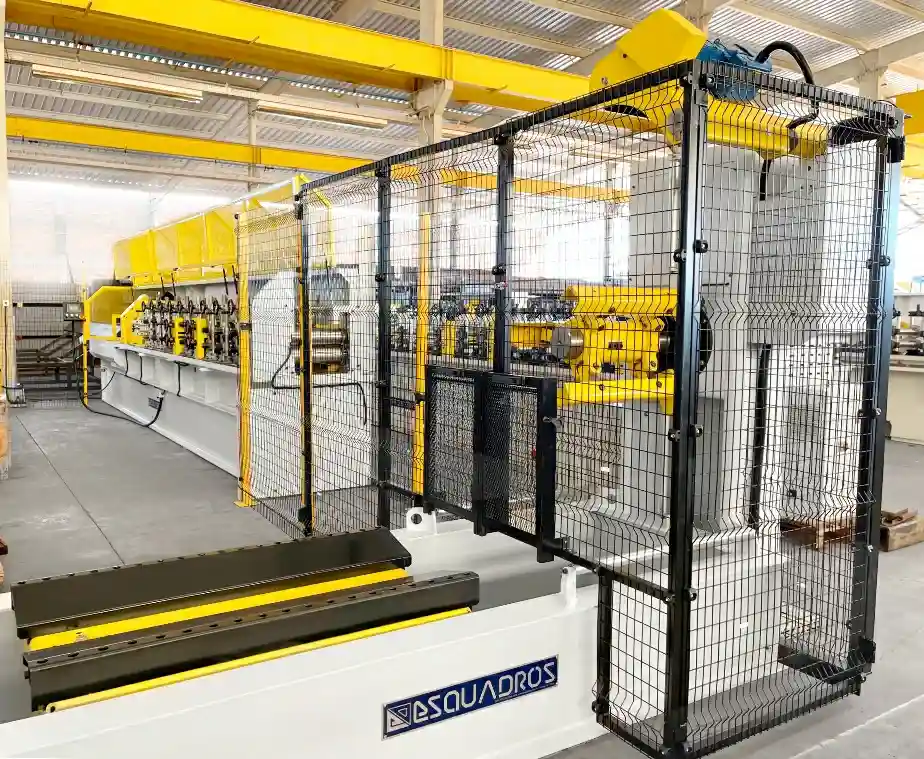
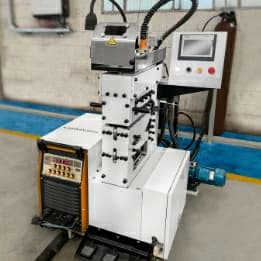
CUTTING AND WELDING (SPLICING) STATION FOR THE ENDS OF THE STRIP
FIND OUT MORE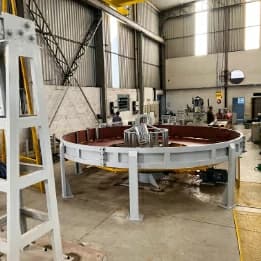
VERTICAL OR HORIZONTAL STRIP ACCUMULATOR
FIND OUT MORE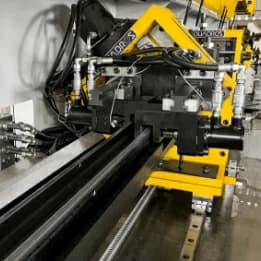
STAMPING MODULES IN INTELLIGENT FLIGHT WITHOUT STOPS (VERTICAL AND LATERAL)
FIND OUT MORE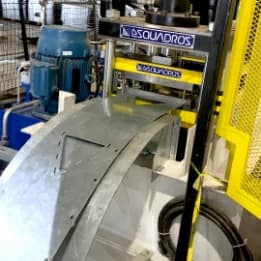
STAMPING BENCH PRIOR TO CONFORMATION
FIND OUT MORE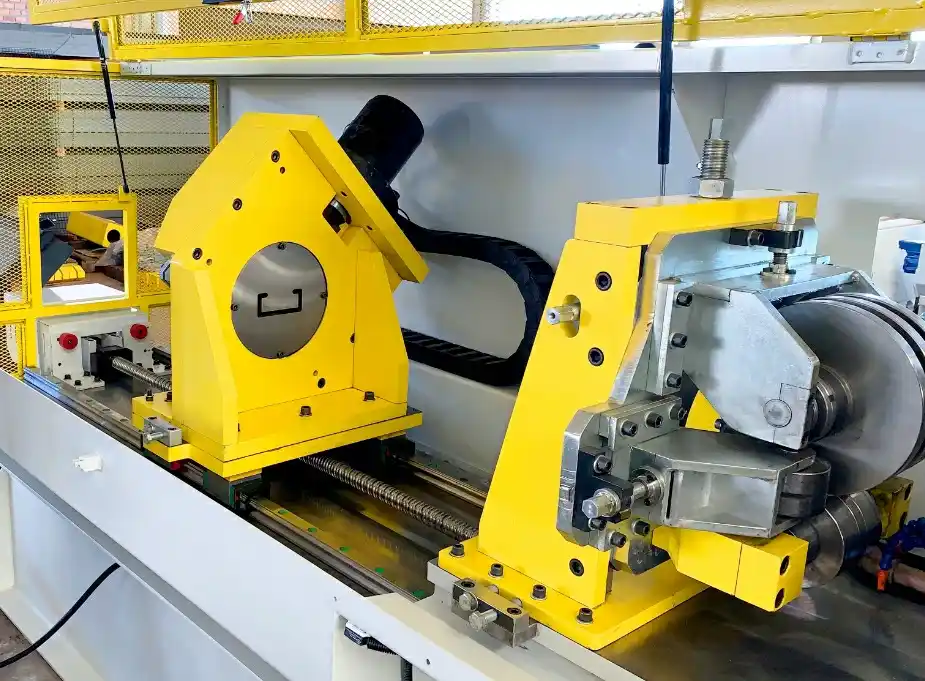
EVOLUTION
For customers who already produce folded sheet metal profiles (UDC) using the conventional cutting and folding process (shears and folding machines), the investment in the Esquadros® Purlin Rollforming Machines will result in greater production capacity and a drastic reduction in operating costs, through:
• Increased productivity;
• Constant precision and quality;
• Optimizing the use of materials - eliminating scraps;
• Lower costs for acquiring materials from coils;
• Less space required for storing materials - coils;
• Easier production planning and control (PCP).
The greater supply of profiles on the market, made possible by the production capacity of the Esquadros® Purlin Rollforming Machines, could lead to increased sales, higher turnover and consequently higher profits for the business.
MAIN FEATURES
• Profiles produced in accordance with Brazilian standard NBR 6355;
• Fully compliant with safety standard NR-12;
• Coils of up to 6 tons;
• Thicknesses from 2.00 to 3.20 mm;
• Actual speed of up to 60 m/min;
• Profiles from 2" to 8" on the same machine (from the U-45x17 mm profile to the C-200x75x25 mm profile);
• Heat-treated, rectified and polished conformation tooling. All parts of the conformation tooling with laser-engraved identification;
• Turret head enables lateral, vertical, longitudinal deflection, transverse deflection and profile torsion calibration;
• Hydraulic guillotine sliding on linear guides and driven by a servomotor rigidly coupled to a ball screw with precision bearings, which cuts without stopping. Guillotine knives made from D2 tool steel, with a cutting profile cut by wire electroerosion with a receiving angle;
• The conformation cooling system includes gutters, ducts, pipes, reservoir and suction pump;
• Flexible hoses with "loc line" joints at each stage to direct the cooling;
• Drive by a group of high-performance, low-backlash geared motors coupled directly to the machine shafts and controlled by a frequency inverter. Synchronized transmission in all conformation stages by chains. First stages with top rollers driven by toothed gears;
• 100% national design, manufacture and technical assistance;
• Technical delivery to the customer's premises by our technicians;
• Complete machine documentation;
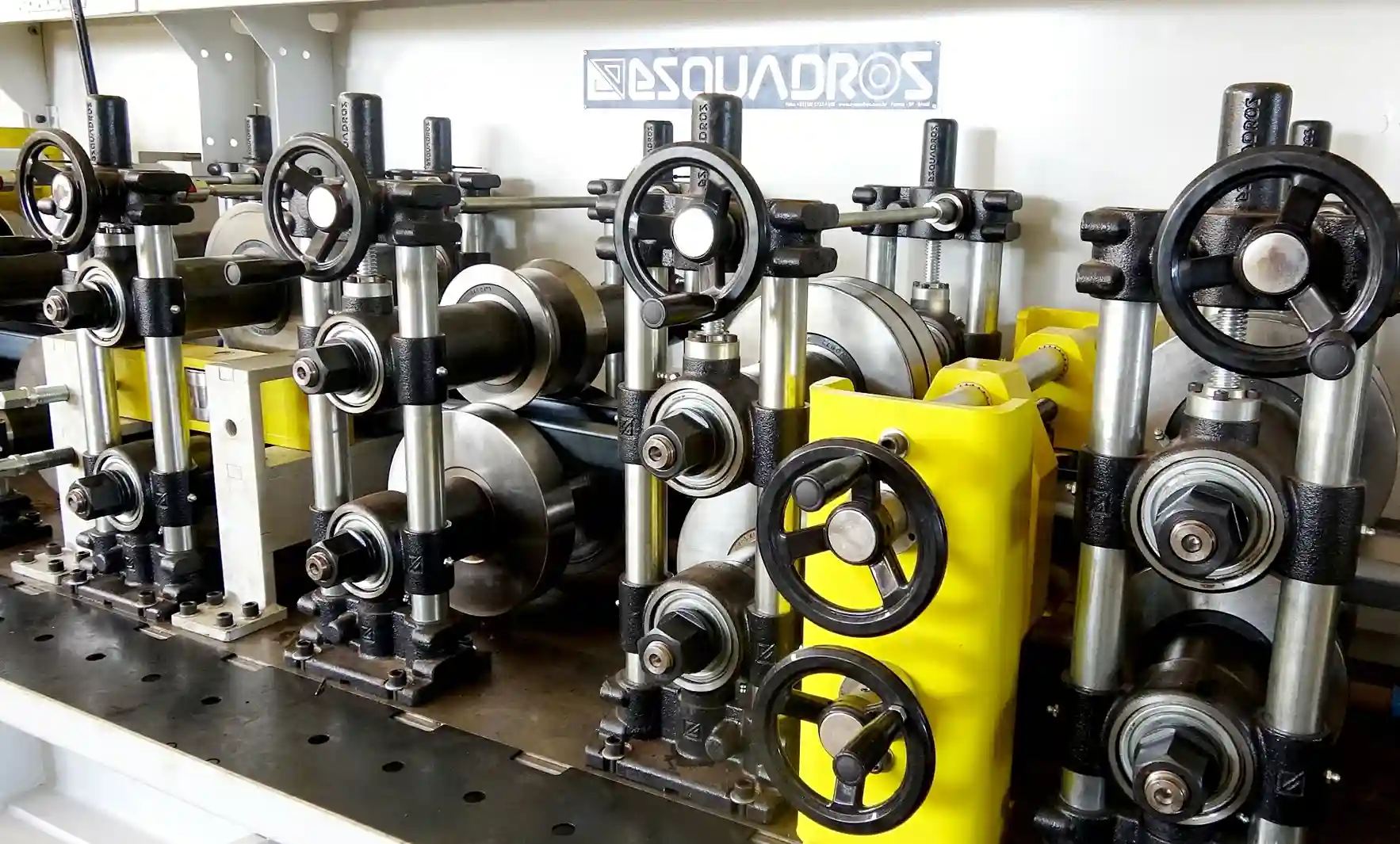
ESQUADROS® DIFFERENTIALS
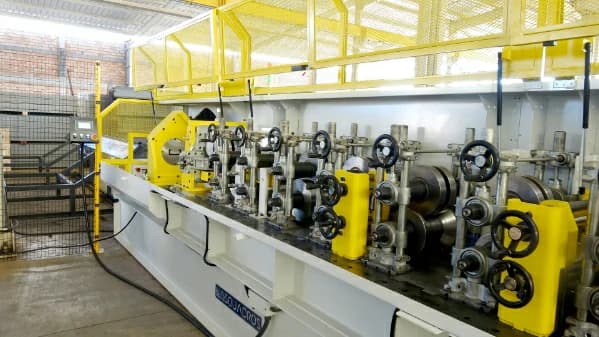
QUICK TOOL CHANGE SYSTEM - UP TO 4X FASTER
Quick-change cylindrical conformation tooling system (up to 4x faster than the conventional system) thanks to the synchronism of the castles and the high precision of the mechanical set.
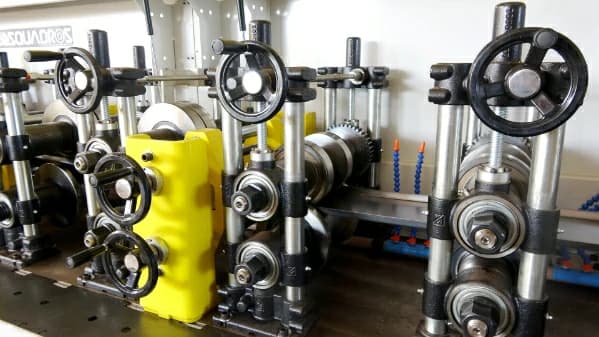
RAPID HEIGHT ADJUSTMENT OF THE UPPER SHAFTS
Synchronized upper bearing height adjustment for very fast setup. Adjusting the height of the upper shaft is done by simply moving a handwheel, which drives two (2) boxes with precision gearboxes, coupled and interlocked, to guarantee a parallel and uniform descent/ascent at each conformation stage, requiring less experience and time from the operator to make adjustments to the profile thickness variations. It also eliminates unnecessary operator movement (a waste of time), since the entire operation is carried out from just one side of the machine, making it more comfortable to operate.
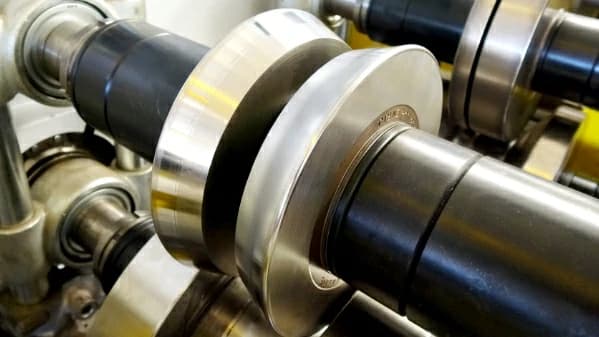
ULTRA-PRECISE CYLINDRICAL CONFORMATION TOOLING
Ultra-precise cylindrical conformation tooling that does not accumulate differences during assembly and eliminates manual adjustments. Spacer bushes to centralize the tooling. All parts are laser engraved for easy identification and assembly. Detailed assembly map for the manufacture of all profiles.
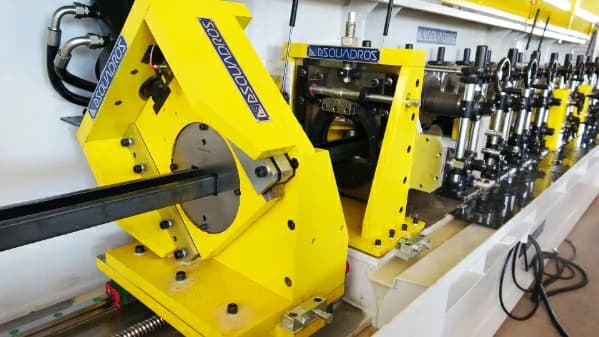
HIGH PRODUCTIVITY WITH SPEEDS UP TO 60 M/MIN
Non-stop cutting through flying cutting by servomotor and drives of the German brand SEW® that achieves actual speed of up to 60 m/min.
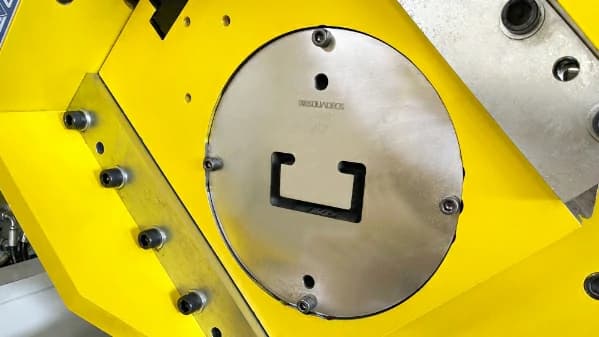
NO-CHIP/SCRAP CUTTING TECHNOLOGY
The shear knives are made of D2 tool steel, with cutting profiles that are cut by wire electroerosion with a receiving angle, for a perfect cut and no burrs. Each profile dimension to be produced has its specific set of knives, with cutting technology that does not generate chips / scrap, that is, higher quality of the final product and elimination of materials waste.
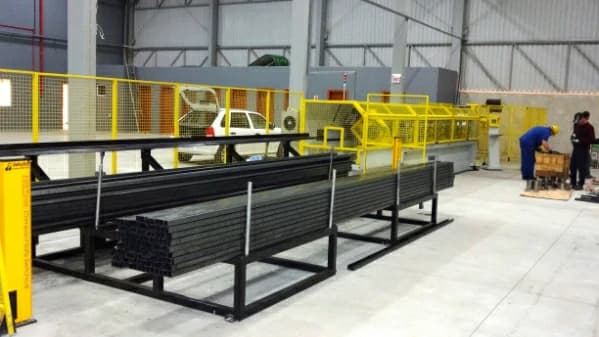
HIGH PRECISION
External encoder from the German brand SICK® with 4096 pulses for measuring the length of the profile operating in a closed loop with the servomotor of the flying cut: guarantee of total precision in the length of the profiles produced.
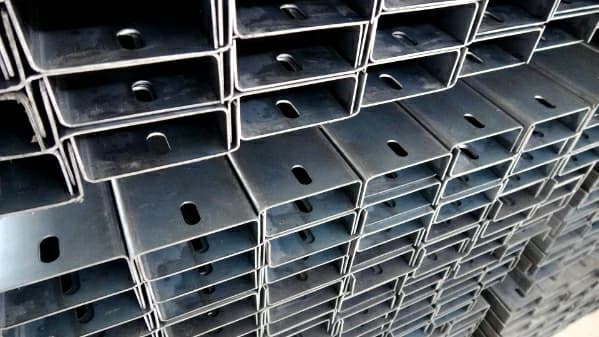
INTELLIGENT FLIGHT STAMPING - NON-STOP STAMPING
Esquadros launches to the market its exclusive technological innovation of "INTELLIGENT FLIGHT STAMPING", which stamps the profiles already formed without stops with maximum precision and productivity, through compact, vertical and lateral stamping modules. It is possible to stamp holes and special cutouts, for the production of the most diverse profiles, such as: metal purlins for civil construction already with mounting holes; profiles for the structure of photovoltaic plates (solar energy generation); among others.
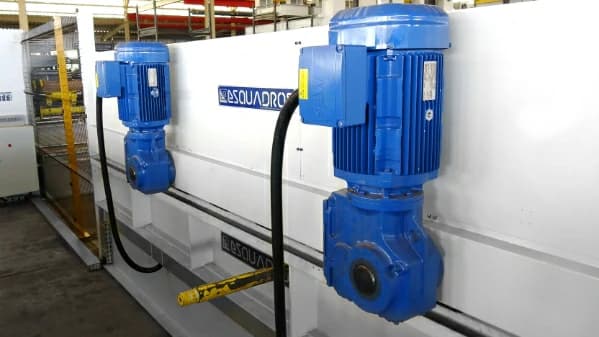
SEW® GEAREDMOTOR GROUP
Drive by a group of energy-efficient geared motors of the German brand SEW® rigidly coupled directly to the transmission shafts. The drives are well dimensioned, providing greater efficiency, minimum energy consumption and sustainability.
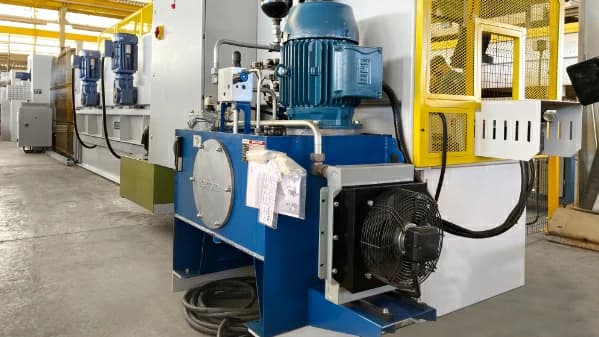
WORLD-CLASS COMPONENTS
BOSCH-REXROTH hydraulic unit, SEW® geared motors, servomotors and electronics, SICK® encoder and sensors, SCHMERSAL® safety devices, SIEMENS® electrical components, among others.
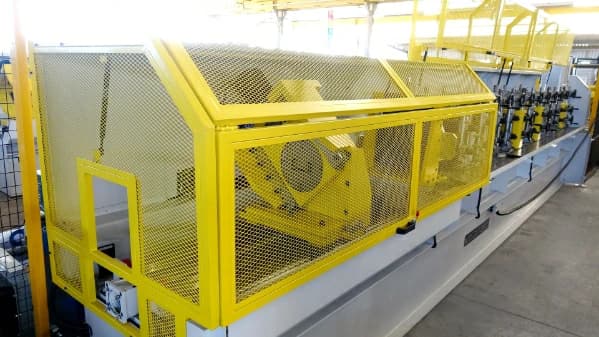
FULL COMPLIANCE WITH THE NR-12 SAFETY STANDARD
Project designed for safe machines according to NR-12.
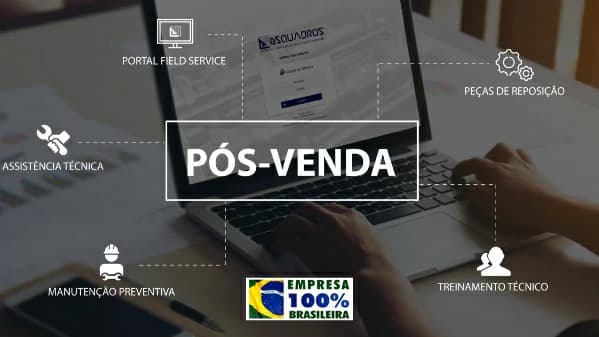
COMPREHENSIVE AFTER-SALES SERVICE
Complete after-sales service with responsiveness, total support for your business throughout the product life cycle, service by technicians and engineers with experience and specialized knowledge, high availability of parts and services.
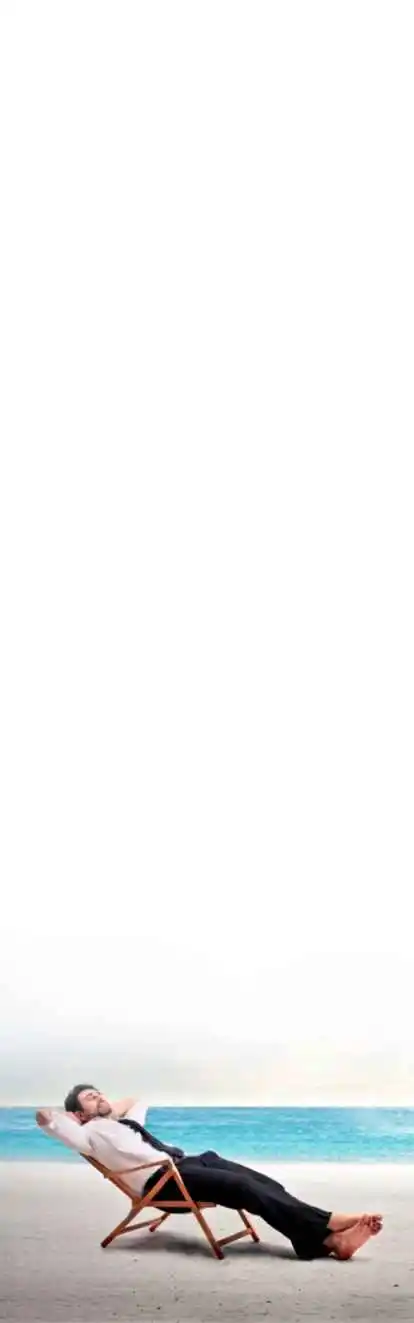
WHY IS ESQUADROS® THE BEST CHOICE?
• Because it is a company that provides permanent technical assistance;
• Because for 36 years Esquadros® has fulfilled all its commitments to customers;
• Because the machines are totally safe according to NR12;
• Because the designs of its machines are technological and perfect;
• Because they are machines tested to exhaustion to ensure quality and performance;
• Because the components are from brands such as Gerdau, Arcelor Mital, Siemens, SEW, SICK, Schmersal, Belgo Bekaert, etc;
• Because the customer receives the machine within the contracted period;
• Because the prices have the best cost x benefit ratio and the machines pay for themselves;
• Because Esquadros® guarantees the exchange for a superior model according to the needs of the customer's business growth;
• Because they have all the accreditations and financing available in Brazil:
Finame - Leasing - Proger - Cartão BNDES - FCO - FINEP - BANCO DO NORDESTE
BUY TRANQUILITY FOR YOU
MEDIAS
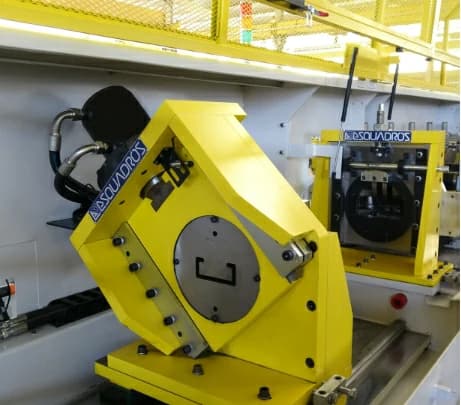
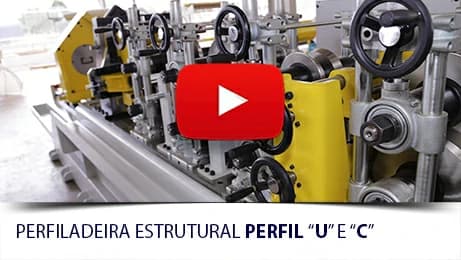
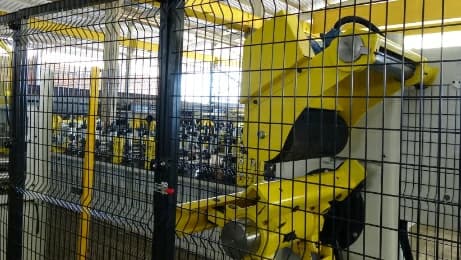
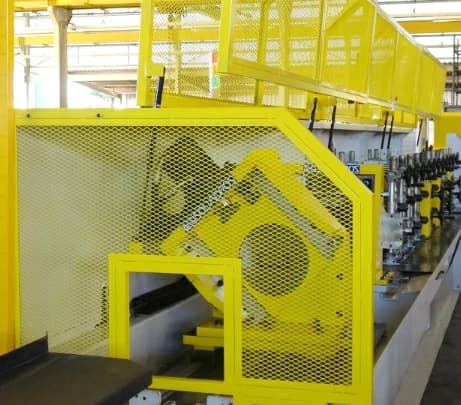
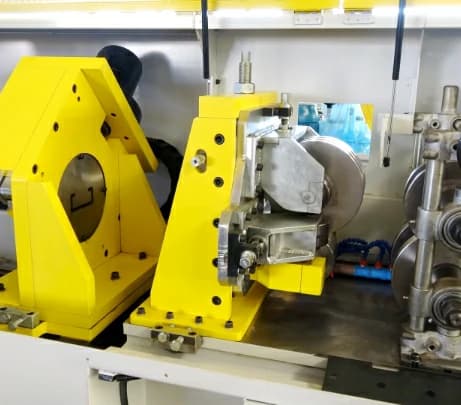
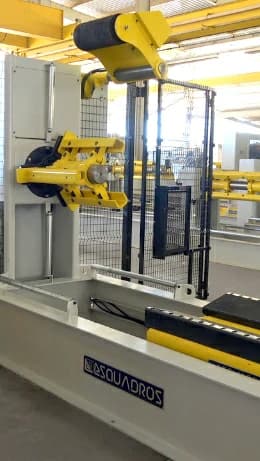
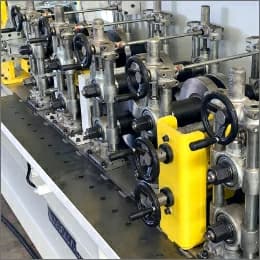
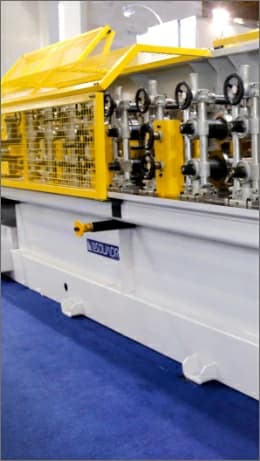
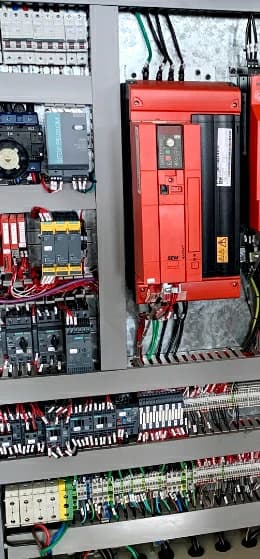
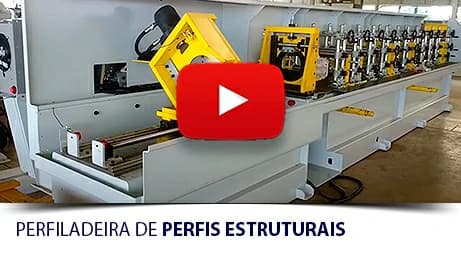
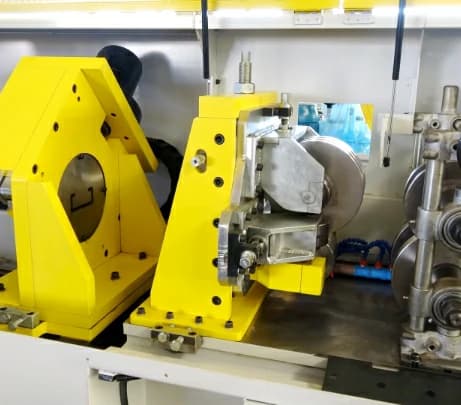
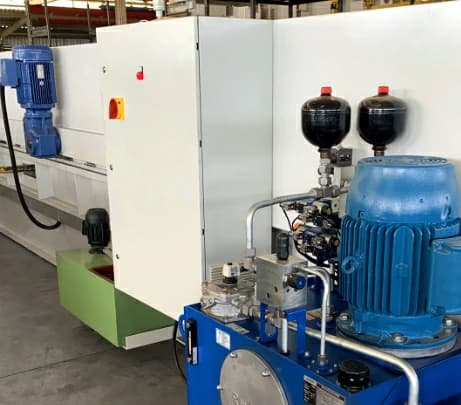
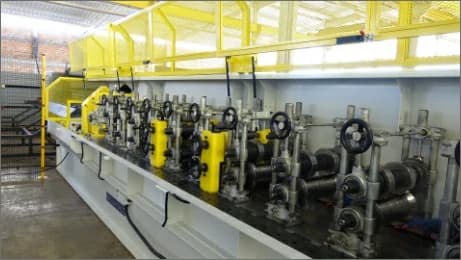
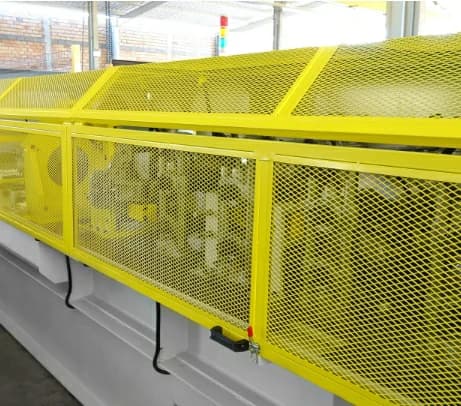
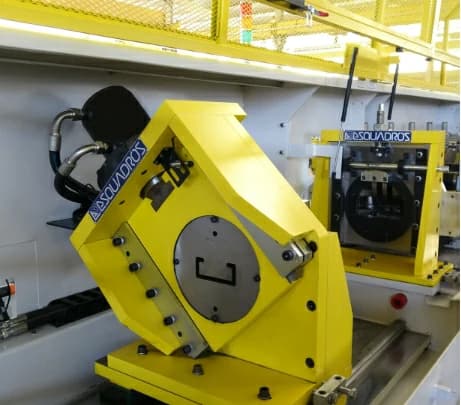
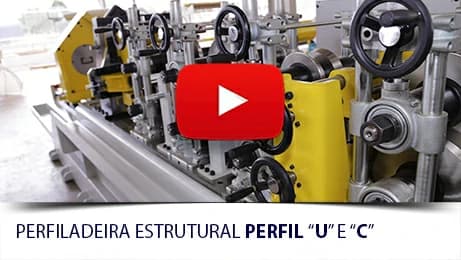
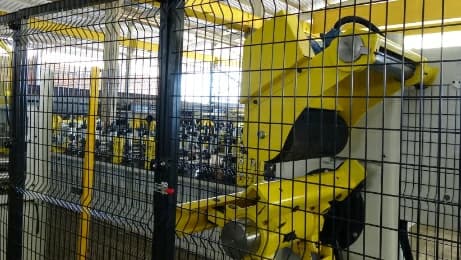
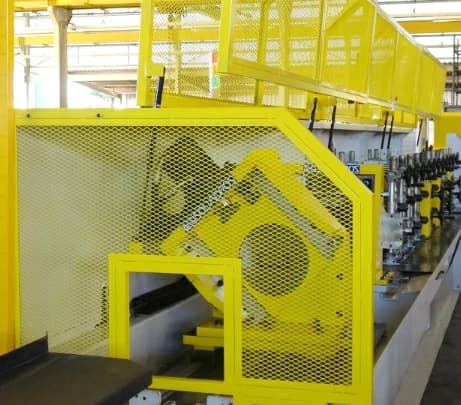
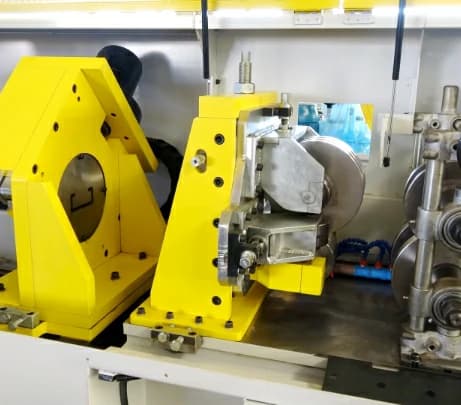
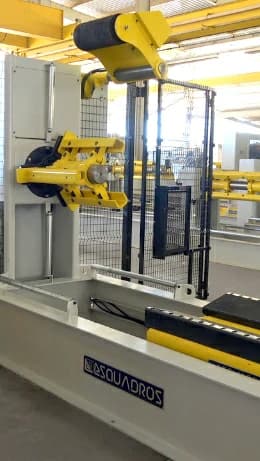
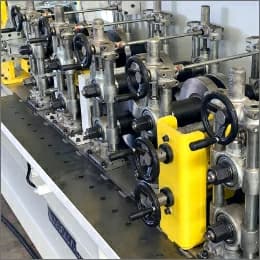
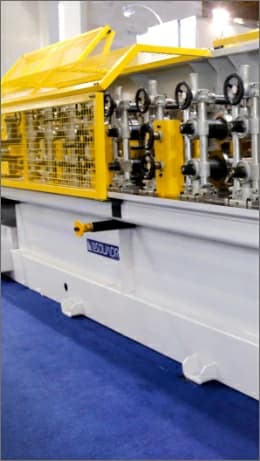
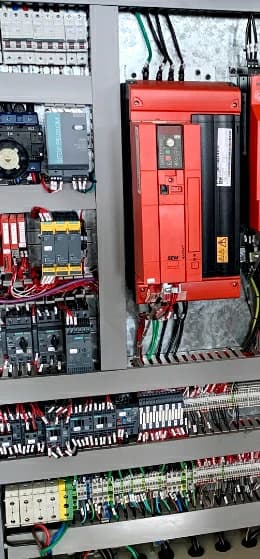
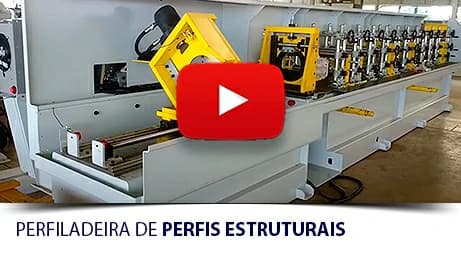
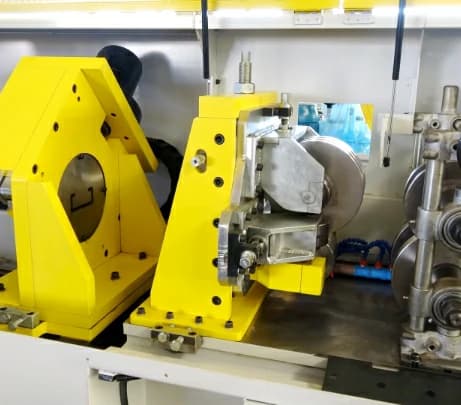
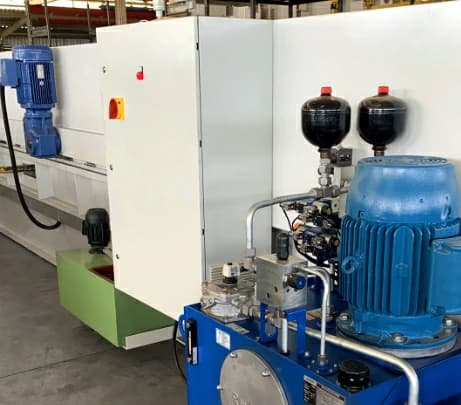
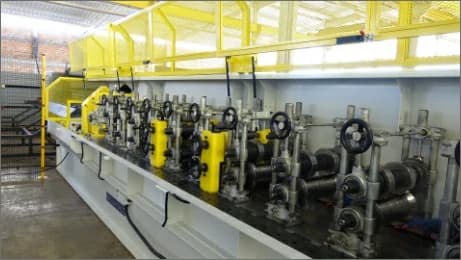
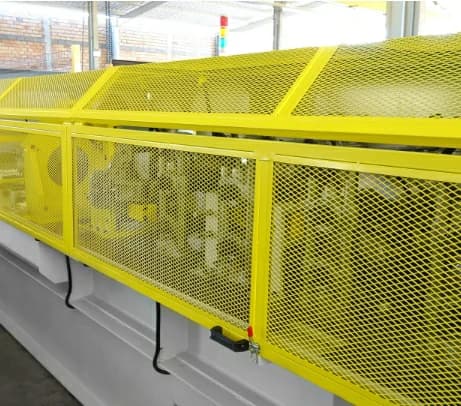
THERE IS
NO COMPARISON
Top of the line components that guarantee performance and
longevity for your equipment.
WHAT MAKES A
MACHINE A ESQUADROS®?
Modern machines with an innovative concept.
State-of-the-art in coil processing.

Easy Payment
We are eligible for all
financing available in
Brazil...

Guaranteed Exchange
We guarantee an exchange for a
superior model according to the growth
needs of your business.

Contact Us
Have any questions? Have a chat with an expert
online or call us at:
+55 16 3712 4100.