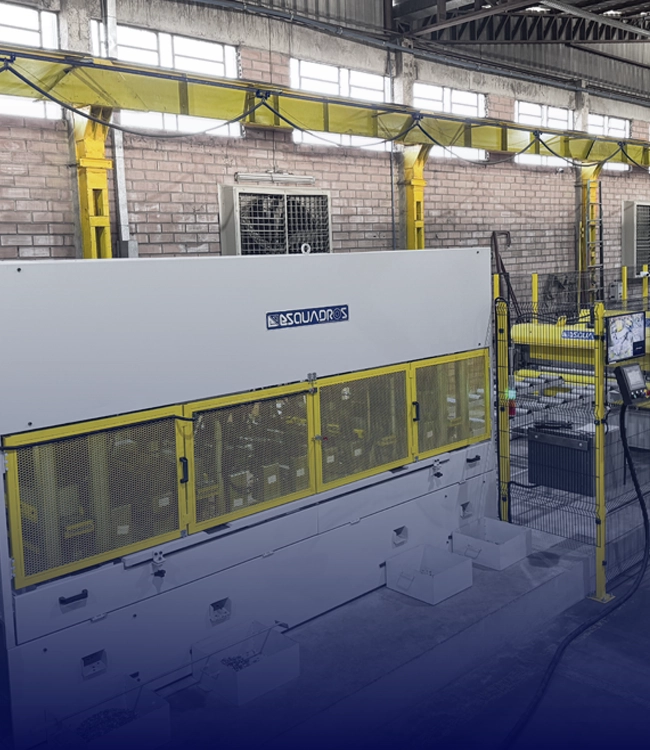
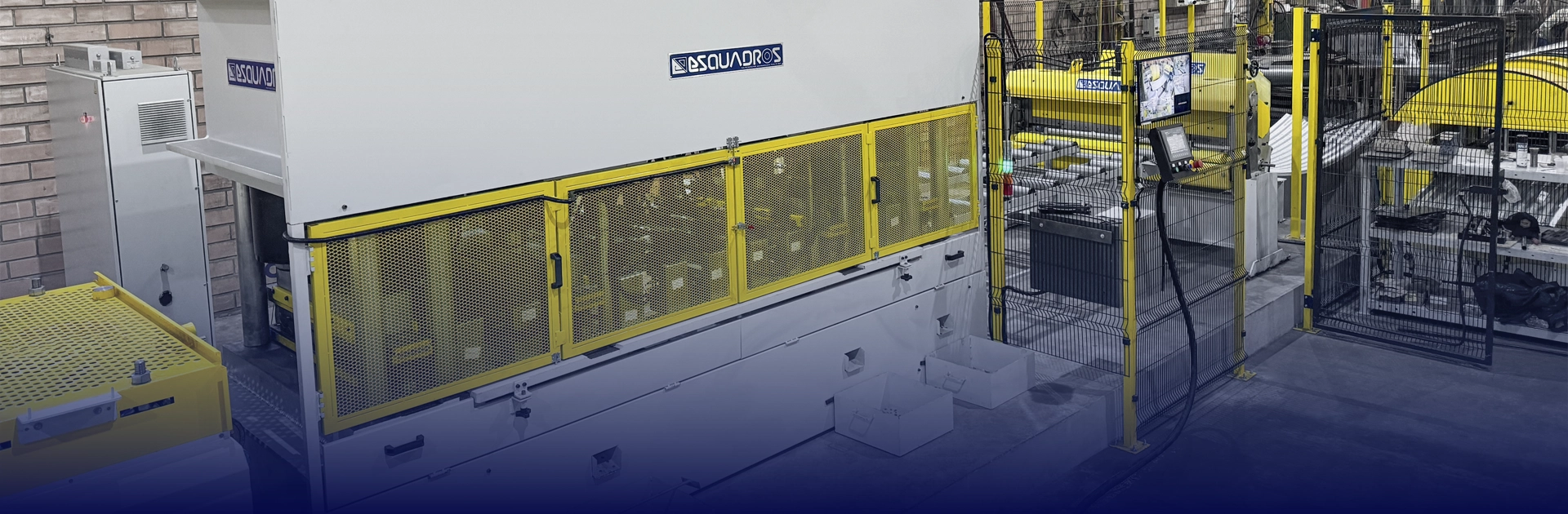
AUTOMATIC STAMPING LINE
FOR SIDE SHEETS (SILO TYPE)
PRO/PREMIUM UNWINDER
The Unwinder has a robust steel structure, welded, and an axle counter-support. The mandrel is made up of three blades that ensure perfect coil fixation. Bearing-mounted supports. By rotating a single nut of the main axle, the mandrel expands its diameter and adjusts to the internal diameter of the coil, ensuring centralized fixation. The machine is coated with epoxy paint in the standard colors RAL 7035 gray and 5Y8/12 yellow.
Technical Specifications | |
---|---|
Load capacity: | 15,000 kgf |
Maximum Yield Strength (L.E.): | 240 N/mm² |
Maximum Tensile Strength (L.R.): | 360 N/mm² |
Maximum width: | 1,300 mm |
Maximum external diameter of the coil: | 1,200 mm |
Maximum internal diameter of the coil: | 20" |
Drive: | Drag |
Braking: | Manual adjustment |
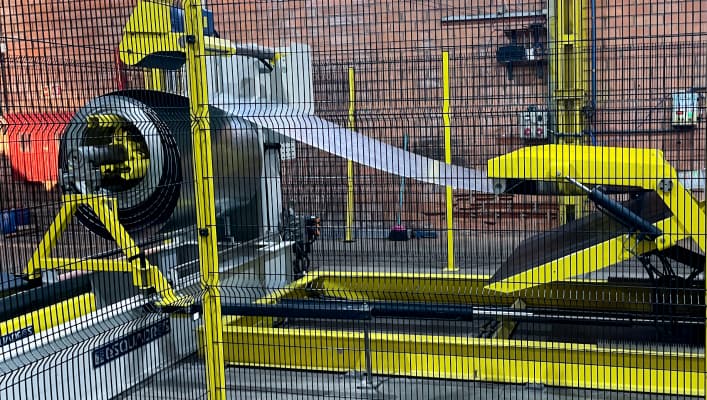

ENTRY TABLE AND STRAIGHTENER
System designed to allow the introduction of the sheet edge into the roll former.
This system consists of:
• Hydraulic lower entry table with a transverse roll;
• Hydraulic upper entry table with pre-bending rolls and a transverse roll;
• Transverse rolls for guiding the sheet height;
• Vertical rolls for lateral sheet guidance.
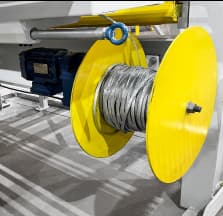
SCRAP REWINDER
Scrap rewinder set. To wind the scrap, the "zig-zag" system distributes the strip evenly on the drums, which are driven by high-efficiency gearmotors with electronic torque control and adjustment. The pneumatic set includes flow control valves and an air preparation unit.
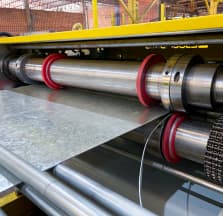
ROTARY SHEAR TR 1600.2
Rotary Shear, coupled model, built with machined, ground, and bolted steel sheets, forming a precise and rigid structure. The rolls are made of special steel alloy, heat-treated and ground, with perfect roundness and exact diameters. Vertical height adjustment with synchronized bearings for precisely parallel movement and easy control. Motorized movement of the bearings. Includes a timing belt with a tensioner to utilize the existing transmission set in the machine.
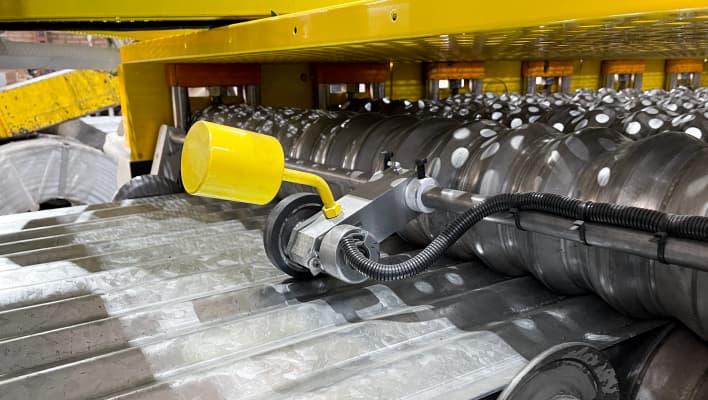
FOR EXISTING ROLL FORMER
Includes gearmotors with brakes, inverters, and control panel for the existing roll former. The customer will be responsible for the mechanical installation of the gearmotors and couplings on the existing shafts.
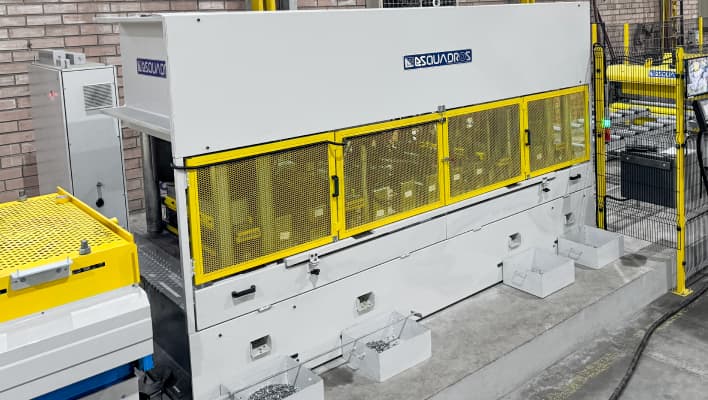
STAMPING BENCH
Bench for stamping silo-type side sheets, perforation as per the technical detailing provided. Holes of Ø9.00 mm, Ø10.50 mm, and Ø13.5 mm.
Technical Specifications | |
---|---|
Thicknesses: | 0.95 ~ 3.04 mm |
Material: | ZAR-400 (T.S. 450 N/mm²) |
Production cycle time: | 30 seconds |
Actual line speed: | 6.10 m/min |
Estimated production: | 120 pieces/hour |
Voltage / Frequency / Duty Cycle: | 380V / 60Hz / 8h |
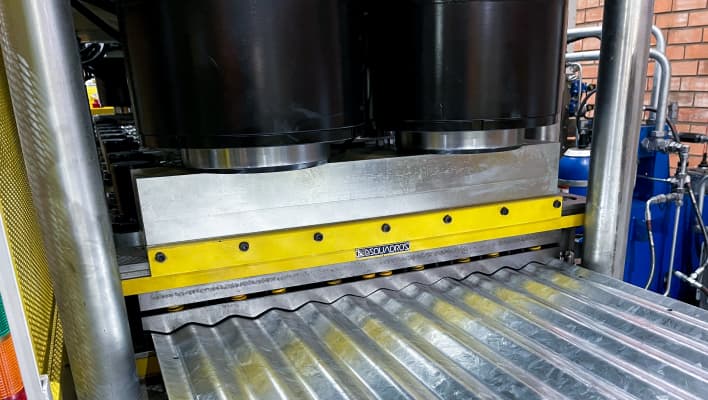
This solution includes a stamping bench for perforating the panels after forming, meeting the customers quality and productivity requirements, as follows:
Technical Specifications | |
---|---|
Cylinder stroke: | 15 mm |
Stamping cycle: | 15 seconds |
Installed capacity: | 900 tonf |
Simultaneous operation: | 350 tonf |
HYDRAULIC SHEAR
Integrated shear. Built from machined, rectified, and bolted steel plates, forming a precise and rigid structure. The vertical movement of the upper blades movable base is driven by hydraulic cylinders. The guides for vertical movement are made using the tangential support of 4 bearings ("stud type track rollers") on each side of the machine, sliding on CNC-machined tracks on the upper blades movable base. Side plates made of polymer eliminate lateral clearance and ensure synchronized descent. Straight blades made of VD2 special steel, with high toughness and excellent ductility, vacuum tempered and quenched, rectified, ground, and polished, ensure precision and low dimensional tolerance in sheet cuts. The base of the lower blade is mounted on a machined channel on each side, allowing blade clearance adjustments and manual blade replacement. Note: This shear will function to cut at the correct position according to the programmed quantity and length of the order pieces.
Technical Specifications | |
---|---|
Useful width: | 1,600 mm |
Minimum sheet thickness: | 0.90 mm |
Maximum sheet thickness: | 3.20 mm |
Drive: | Hydraulic cylinders |
Number of cutting edges per blade: | 04 |
Maximum yield strength (Y.S.): | 240 N/mm² |
Maximum tensile strength (T.S.): | 360 N/mm² |
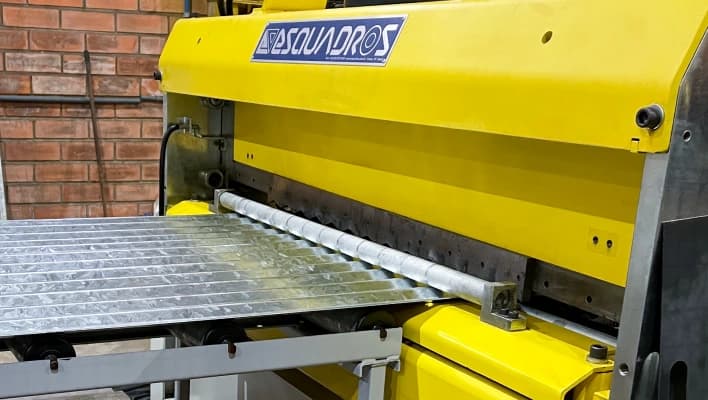
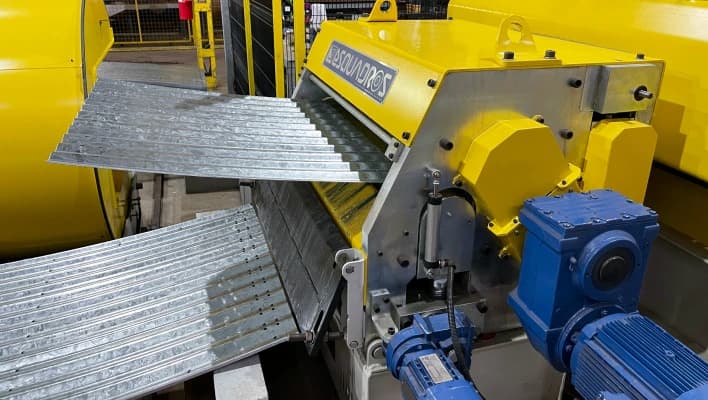
ROLLING MACHINE FOR SILO SIDE BODY SHEET
• Module for rolling metal sheets for silo side bodies. • Rolling is performed before cutting the pieces to achieve the desired curvature radius uniformly along the pieces section. • Rolls made of alloy steel, CNC machined with a special profile for rolling silo-type panels. • Automatic and digital adjustment of the rolling rolls for curvature radius setup. • Integrated hydraulic shear system for cutting the sheet after rolling. Includes digital and automatic CNC drive for curvature adjustments and calender operation. Absolute encoder for electronic position control.
TILTING DEVICE
Esquadros® tilting solutions ensure smooth and safe rotation at angles of up to 90° for coils weighing up to 15 tons. Key benefits: Simple and safe operation; Quick return on investment; Reduced risk of accidents; Low and simple maintenance; Decrease in falls or damage to handled materials. Slit coil tilting device. Articulated movement with a 90° rotation angle, allowing the coil to be supported vertically and positioned horizontally. Driven by a geared motor and chain transmission. Robust "V"-shaped saddle, constructed in electro-welded steel, fixed to the tilting device structure for supporting the coil in the vertical position. All operational functions of the tilting table are controlled through the control panel. The machine is coated with epoxy paint in the standard gray RAL 7035 and yellow 5Y8/12 colors.
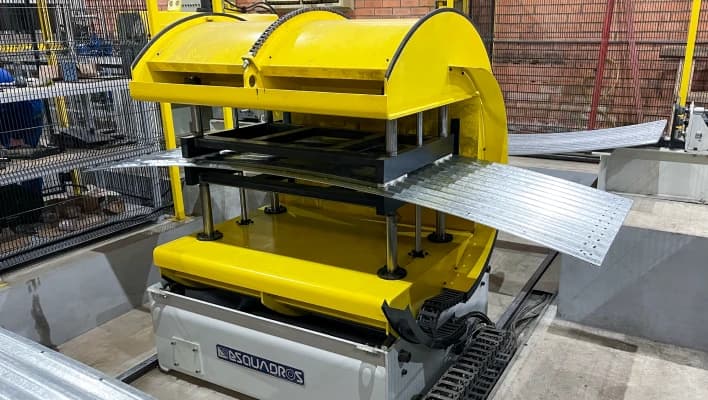
LINE COMPOSITION
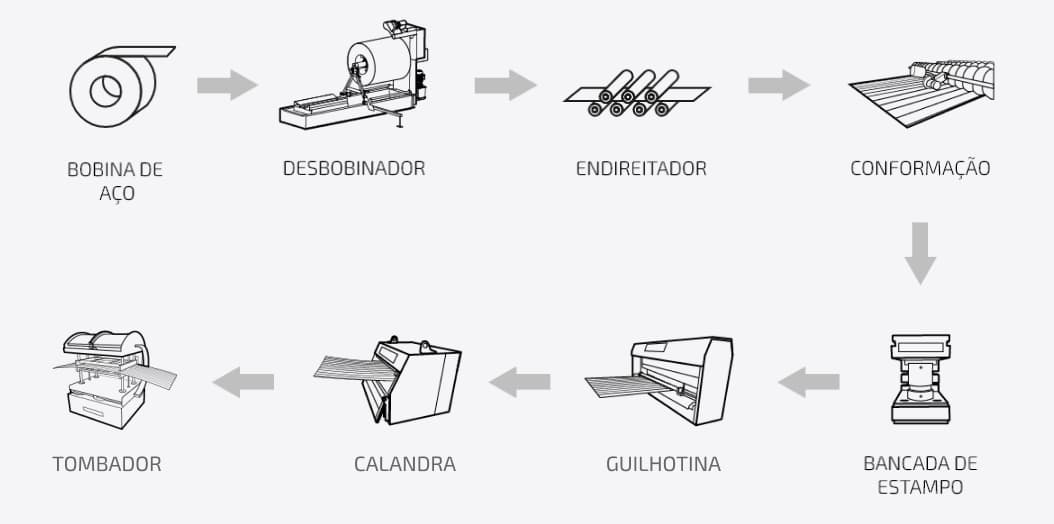
MÍDIAS
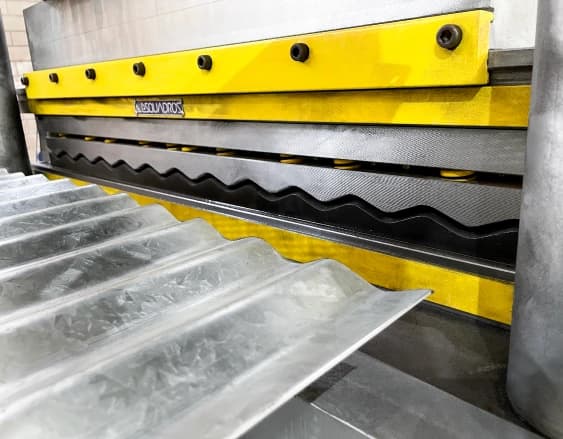
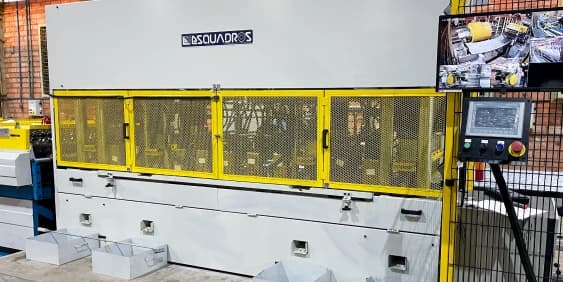
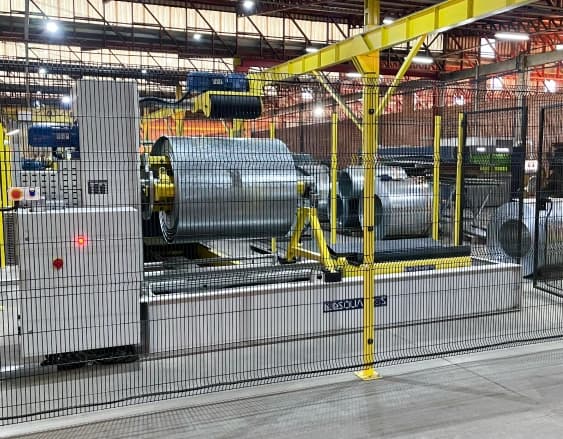
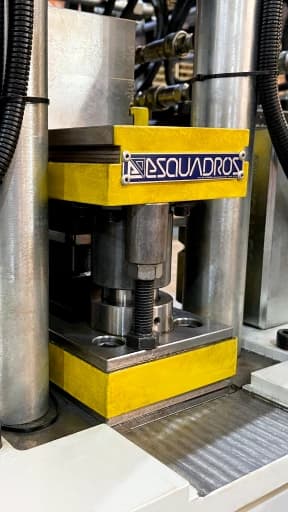
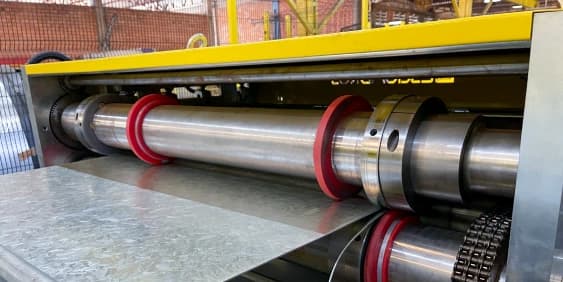
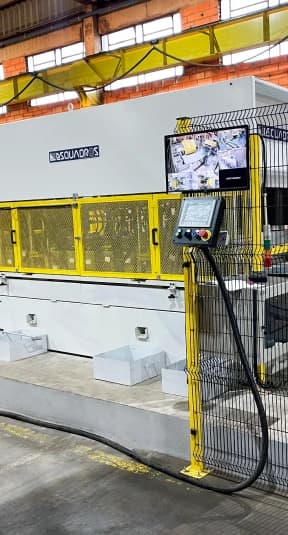
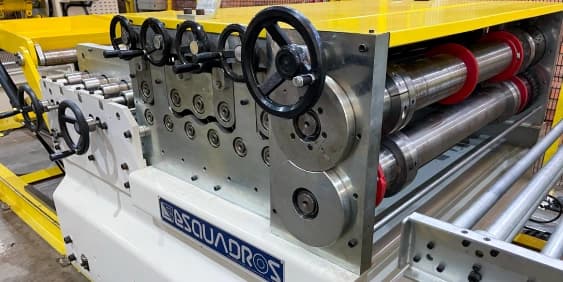
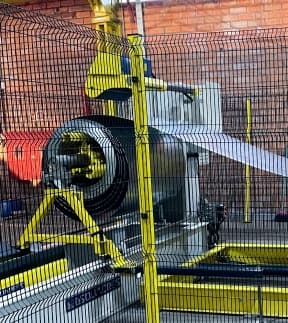
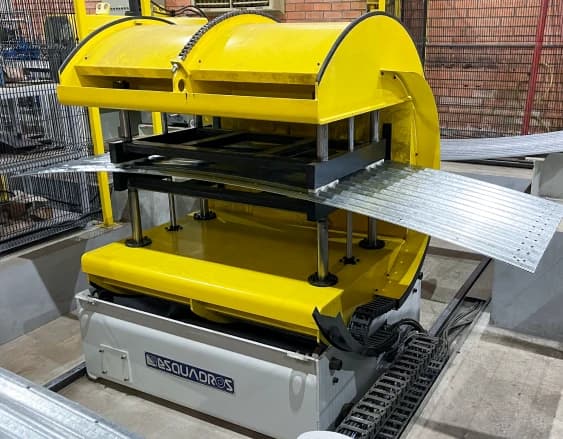
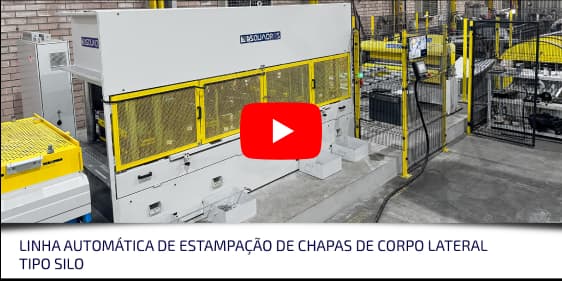
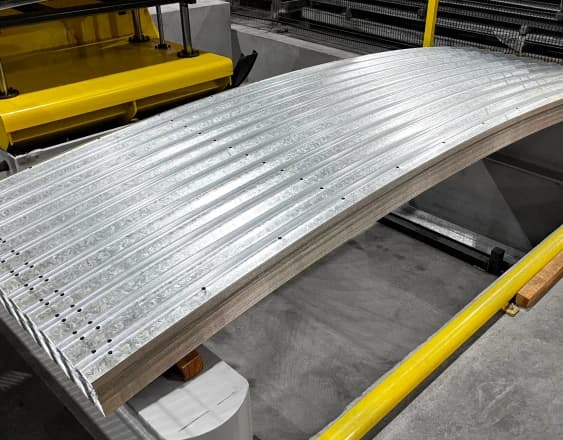
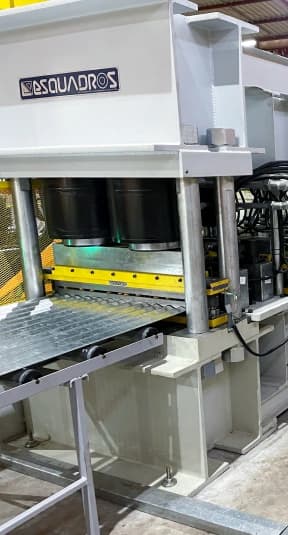
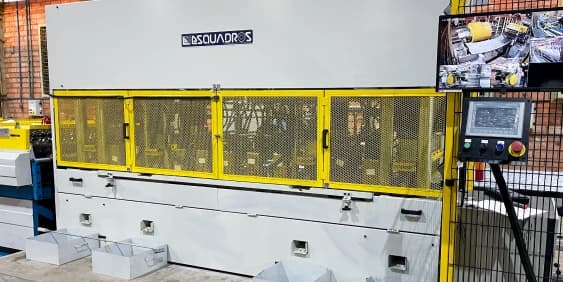
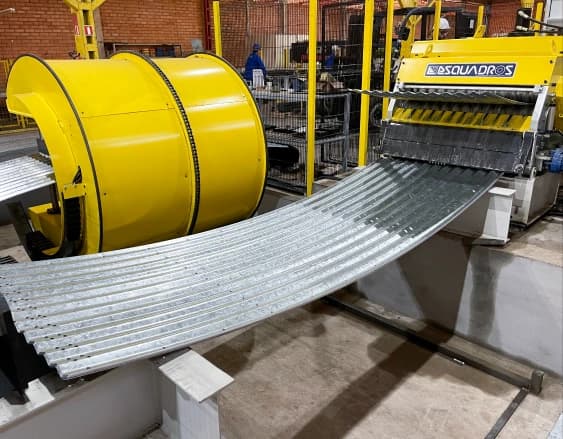
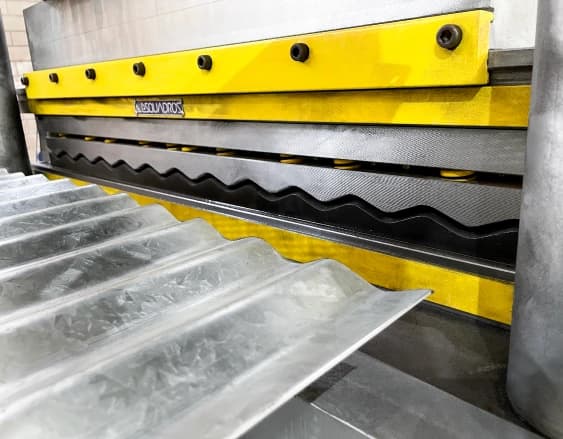
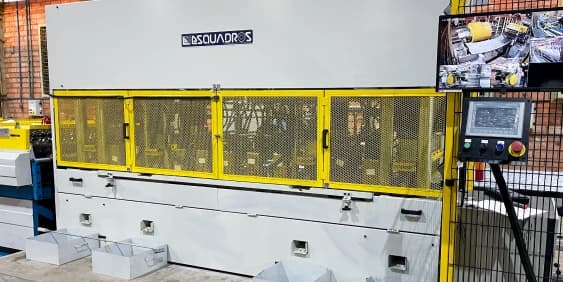
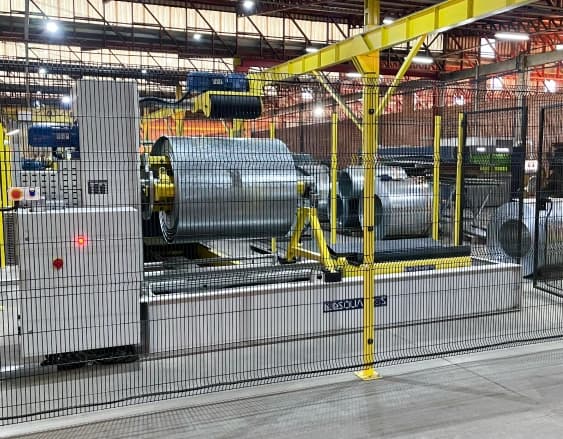
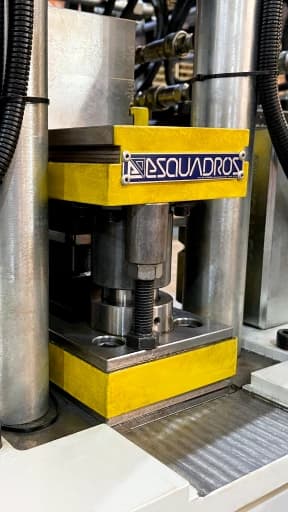
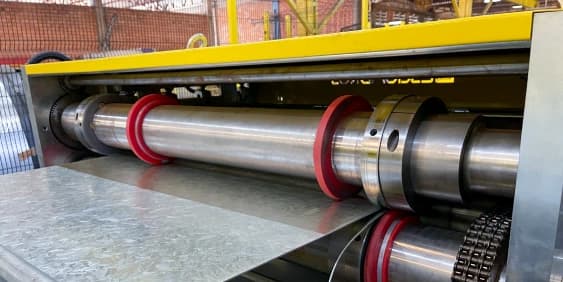
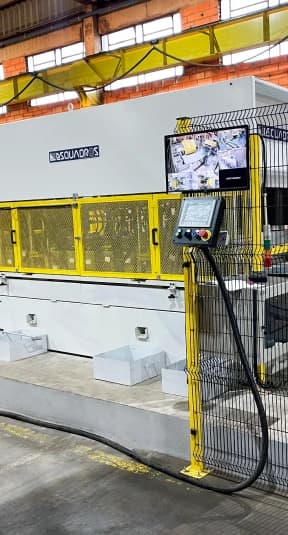
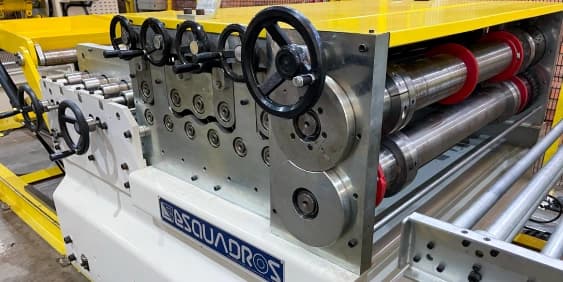
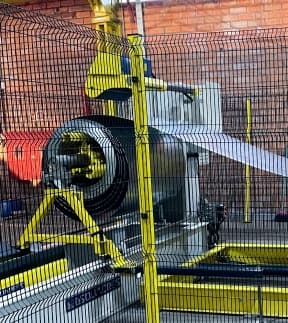
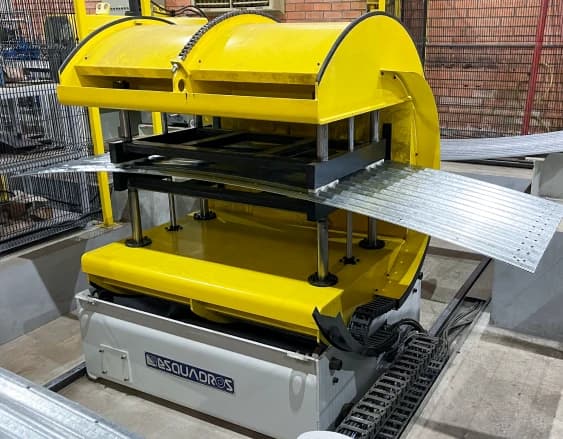
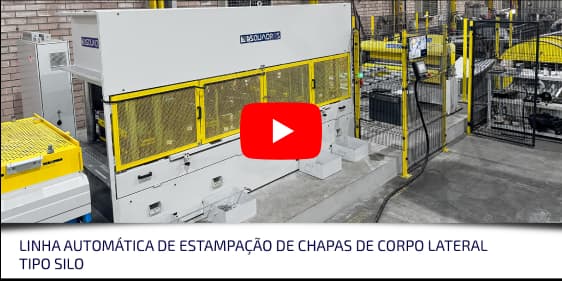
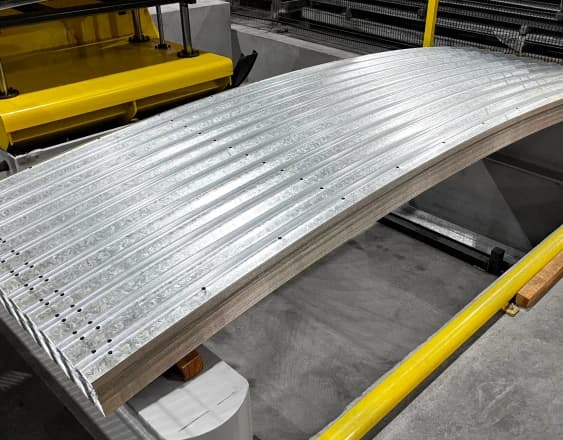
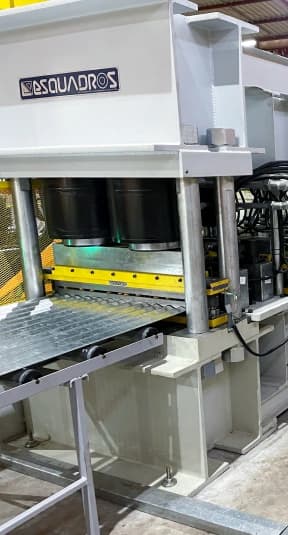
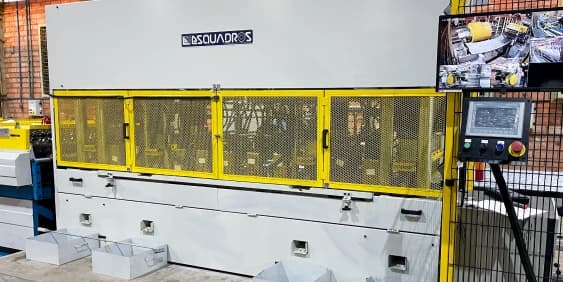
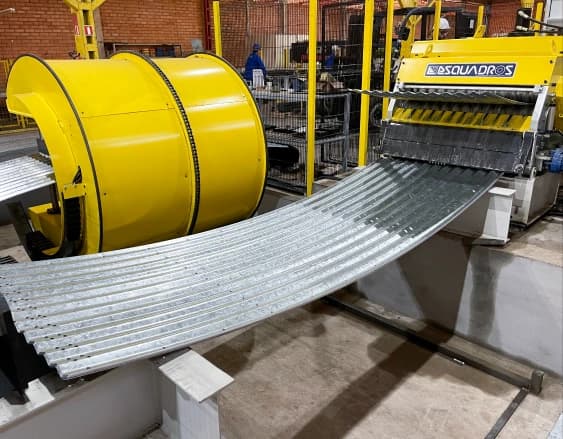
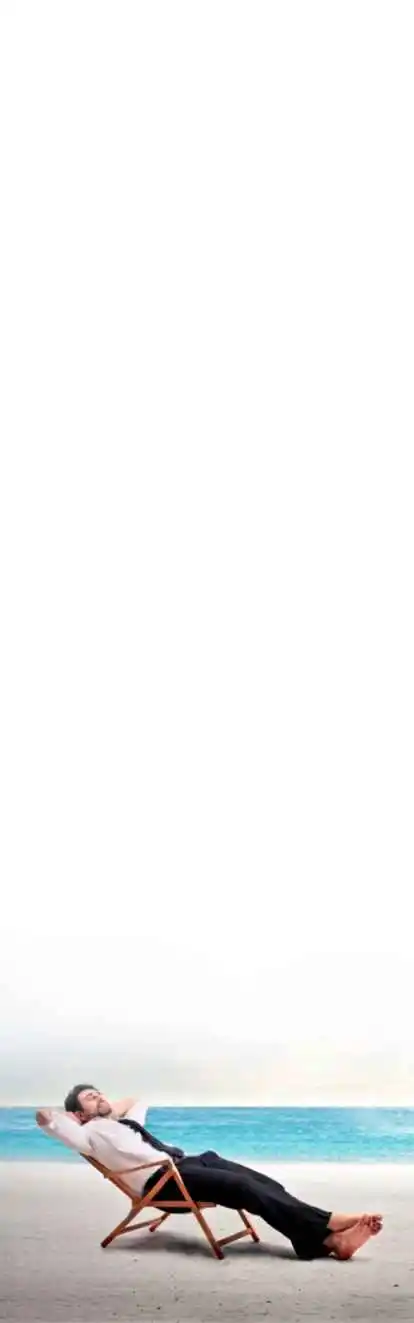
WHY IS ESQUADROS® THE BEST CHOICE?
• Because it is a company that provides permanent technical assistance;
• Because for 36 years Esquadros® has fulfilled all its commitments to customers;
• Because the machines are totally safe according to NR12;
• Because the designs of its machines are technological and perfect;
• Because they are machines tested to exhaustion to ensure quality and performance;
• Because the components are from brands such as Gerdau, Arcelor Mital, Siemens, SEW, SICK, Schmersal, Belgo Bekaert, etc;
• Because the customer receives the machine within the contracted period;
• Because the prices have the best cost x benefit ratio and the machines pay for themselves;
• Because Esquadros® guarantees the exchange for a superior model according to the needs of the customer's business growth;
• Because they have all the accreditations and financing available in Brazil:
Finame - Leasing - Proger - Cartão BNDES - FCO - FINEP - BANCO DO NORDESTE
BUY TRANQUILITY FOR YOU
THERE IS
NO COMPARISON
Top of the line components that guarantee performance and
longevity for your equipment.
WHAT MAKES A
MACHINE A ESQUADROS®?
Modern machines with an innovative concept.
State-of-the-art in coil processing.

Easy Payment
We are eligible for all
financing available in
Brazil...

Guaranteed Exchange
We guarantee an exchange for a
superior model according to the growth
needs of your business.

Contact Us
Have any questions? Have a chat with an expert
online or call us at:
+55 16 3712 4100.